Modeclix

Until now, more elaborate, sculptural couture 3D ‘prints’ have graced the catwalk for designers including Iris van Herpen, Chanel and Noa Raviv. One of the biggest challenges with 3D Printing technology to date has been how to make it wearable. This unique project addresses that challenge by ‘printing’ textiles that are flexible with movement and mimic traditional cloth.
The complex design process involved in making these revolutionary garments represents a huge breakthrough for garment technology and 3D printing. The project focuses on an interpretation of weave, stitch and knit. The initial prototypes are 3D printed as pieces of textile that have enough movement to ensure that they are fluid and represent a ‘fabric’ that can be used to make a garment. Featuring eight dresses and two headpieces this collection is the first to make 3D concepts wearable and can be customised to any size and shape either before printing or after, by adjusting the intricate links to fit by hand. They can also be dyed in an endless spectrum of thousands of colours. The collection, designed to flatter ones natural shape without compromising on style or comfort, was premiered at the Mercedes-Benz Bokeh South Africa International Fashion Film Festival. The fashion film ‘Molly Makes a Dress’ was nominated for two awards; Best Fashion and Best Film.
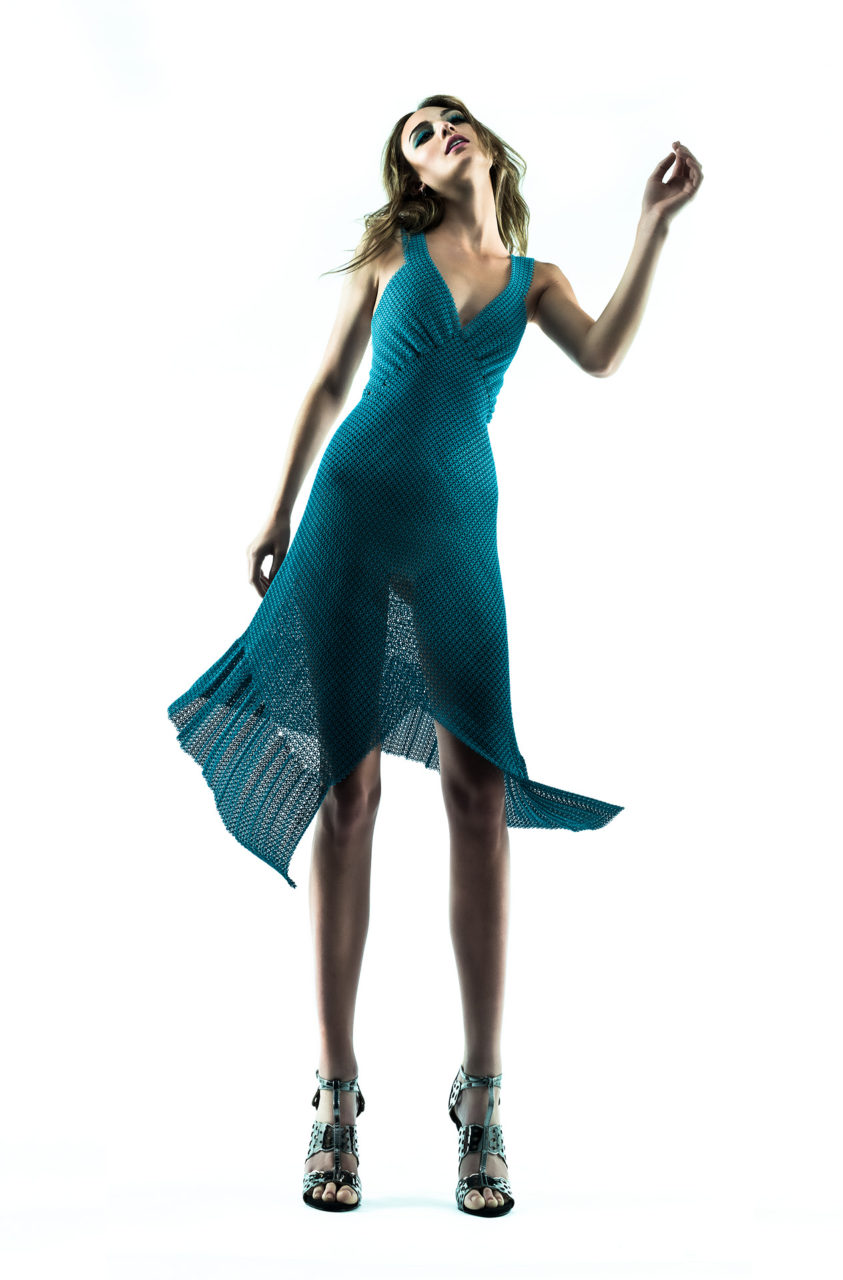
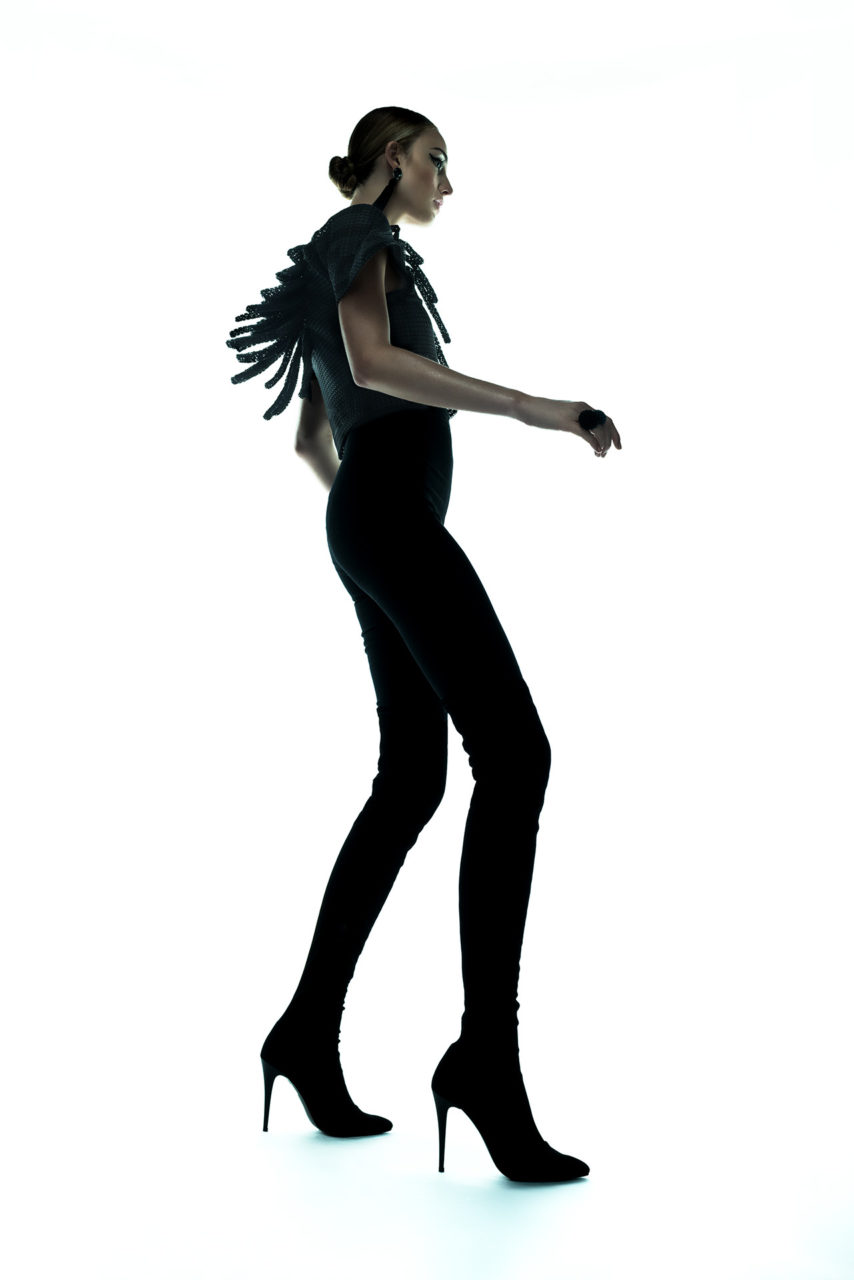
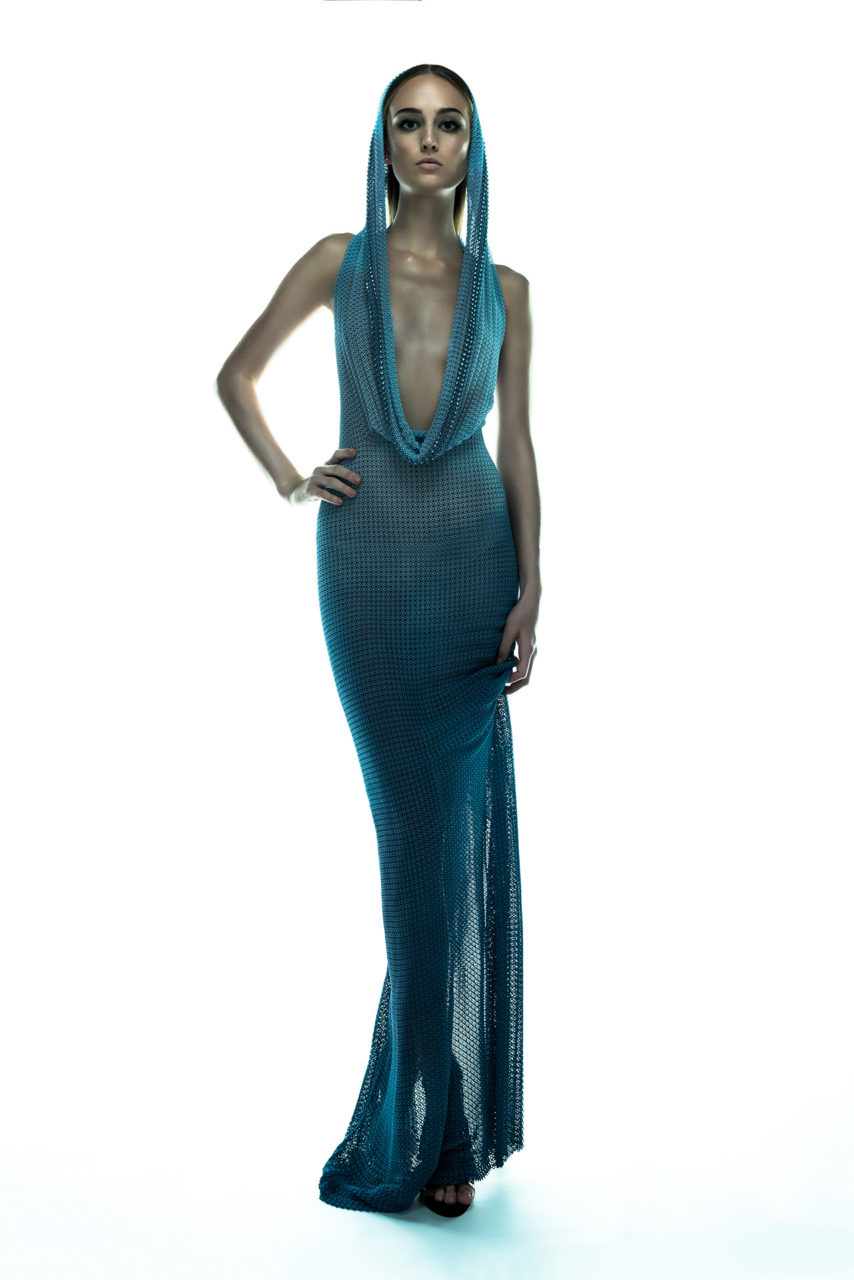
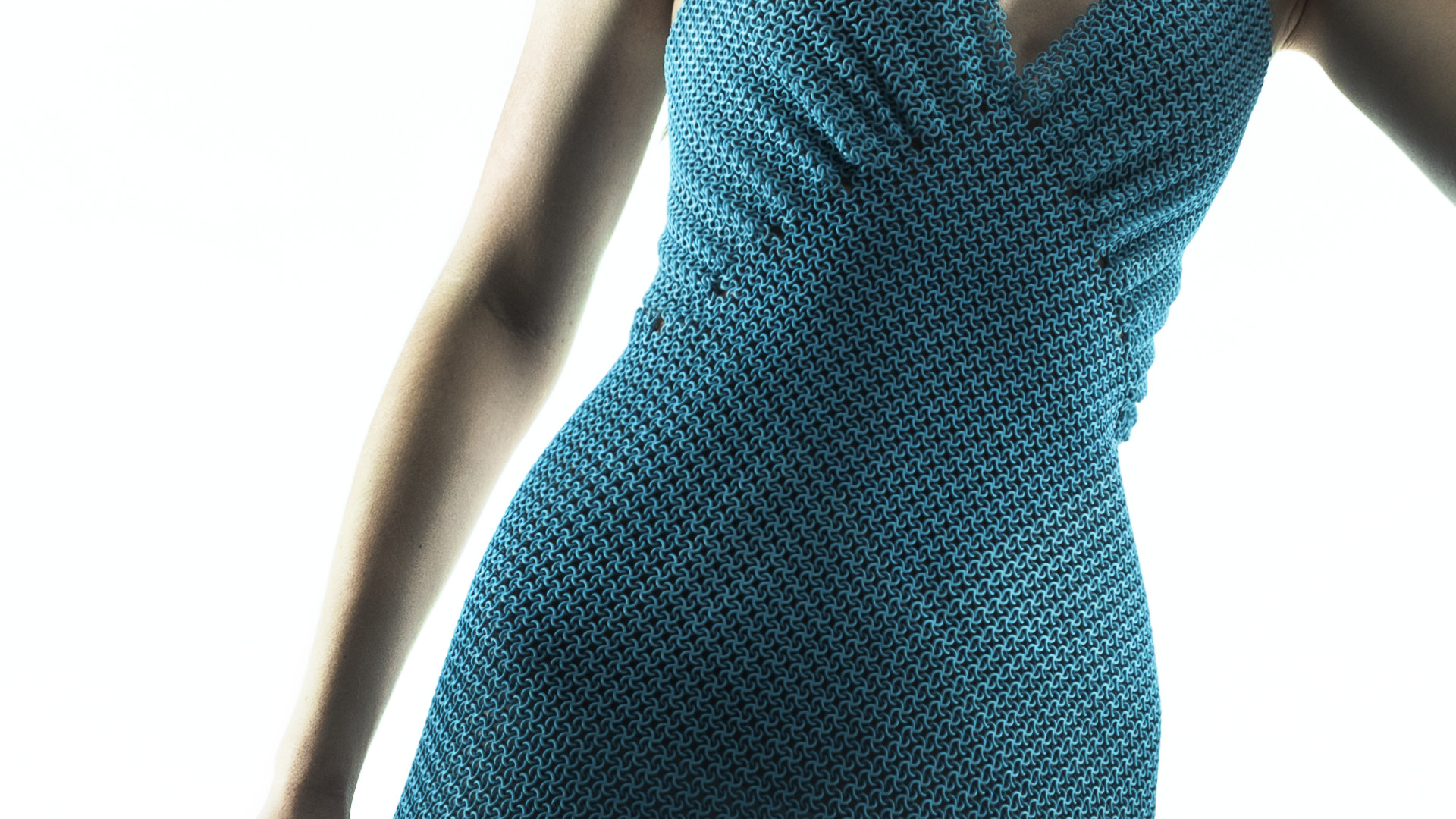
I’ve spent the last 25 years exploring how technology and 3D printing can enhance production techniques for jewellery and accessories, and this has been a fantastic opportunity to take this research even further. There is a huge amount of potential to develop complex construction techniques that defy traditional pattern cutting and create garments that are multi-functional, customisable and wearable.
Mark Bloomfield, Managing Director of electrobloom
The collection is available to view online:
It is also available to view in store at:
electrobloom
Studio 2.11
Oxo Tower Wharf
Bargehouse Street
London